1) shaft design. Increase the number of shaft support bearings, reduce the support spacing, in the appropriate range to reduce the length of the shaft, the appropriate increase in the diameter of the shaft, increasing the shaft stiffness; when the fire pump shaft speed gradually increased and close to or integer times the pump rotor inherent Vibration frequency, the pump will violently vibration up, so in the design, should make the natural frequency of the drive shaft to avoid the motor rotor angular frequency; improve the manufacturing quality of the shaft to prevent mass eccentricity and excessive form and position tolerance.
2) the choice of sliding bearings. The use of non-lubricating bearings; in liquid hydrocarbons and other chemical pumps, the sliding bearing material should be used with good self-lubricating properties of materials, such as PTFE; in the deep well water pump, bushing choice of PTFE filled PTFE , Graphite and copper powder material, and rational design of its structure, so that the sliding bearing fixed and reliable; impeller seal ring and the pump seal ring friction factor used in a small friction pair, such as M20lK graphite material a steel; limit the maximum speed; Bearing capacity and bearing seat rigidity.
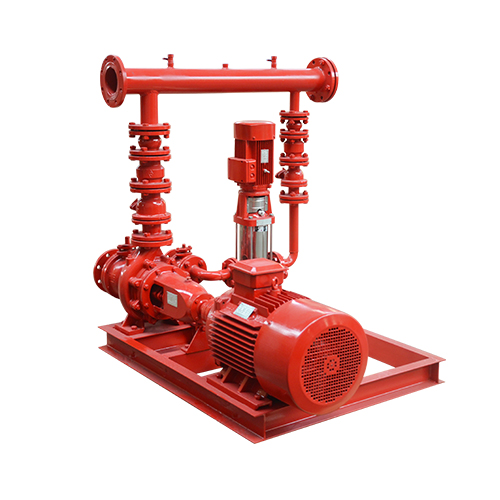
3) Use a stress relief system. For the delivery of hot water pump, the design should be made by the pump deformation caused by the structural stress between the connectors to be released, such as bolts in the bolts above the bolts to increase the pump to avoid direct and very large stiffness Basic contact.
2. Water pump design considerations
1) the rational design of pump impeller and flow channel.
2) Cavitation vibration is a very important part of pump vibration.
In order to ensure that the suction pipe or pressure water pipe without air accumulation, any part of the suction pipe can not be higher than the pump inlet. In order to reduce the pressure pulsation at the nozzle, the diameter of the suction pipe should be larger than the diameter of the pump population by one order of magnitude, so that the flow of water in the pump population has a certain contraction, the velocity distribution is more uniform, but also in the pump population before a Straight pipe, straight pipe length of not less than 10 times the pipe diameter.
Note to create a good water conditions, into the pool water flow should be smooth and uniform, in order to eliminate the vibration associated with the Carmen vortex.
3) Basic design. The basis weight should be more than three times the mechanical weight of the pump and the motor; the foundation of the sump should be of sufficient strength; the motor bracket and the base are preferably made integral or in surface contact; set between the pump and the stand Vibration isolator or vibration isolator. In addition, the use of damping material between the pipe connections to reduce the pipeline layout, can eliminate the elastic contact and hydraulic loss caused by vibration.
3. From the installation and maintenance process as a method to eliminate pump vibration
1) Shaft and shaft system. Before installation, check the pump shaft, motor shaft, the drive shaft is not bending deformation, the quality of eccentricity, if any, you must correct or further processing; check with the guide bearing contact shaft, whether due to bending friction bearing or bushing So that their own by the force. If the monitoring indicates that the shaft is actually bent, correct the pump shaft. At the same time, check the end of the shaft clearance value, if the value is too large, then the bearing has been worn, need to replace the bearing.
2) impeller. Dynamic and static balance is qualified.
3) coupling. Whether the bolt spacing is good; elastic pin and elastic ring combination can not be too tight; coupler bore with the shaft is too loose, if too loose, such as spraying can be used to reduce the coupling diameter until it reaches With the required size, and then fixed on the shaft coupling.
4) bracket and floor. Timely detection of vibration of the fatigue of the support to prevent the reduction of strength and stiffness caused by the natural frequency decreases.
5) Gap and wearing parts. The gap between the impeller and the volute should be adjusted properly; regular inspection and replacement of impeller ring, pump mouth ring, inter-stage bushing, partition bushing and other easy to wear parts.