Mechanical solutions
Mainly through the protective cover and fixture seal flange and the gap flange, usually stainless steel or plastic material with a rubber seal. This type of protection is less flexible and requires the storage of housings or fixtures that are perfectly matched to flanges of various sizes.
Tape or semi-solid with anti-corrosion solution
Roll-wrapped tape is wrapped around the substrate surface for protection. Because the semi-solid polymer has good water resistance, this kind of protection can provide reliable corrosion protection.
Hot melt plastic solutions
Hot-melt plastic is essentially a high-temperature heating waxy fusible polymer, sprayed through the professional hot melt equipment to the substrate surface. This protection has the advantage of re-melting and can be reused, cost savings. However, this approach also requires hot work, professional equipment and construction services, although you can re-use, but difficult to open and sealed during maintenance.
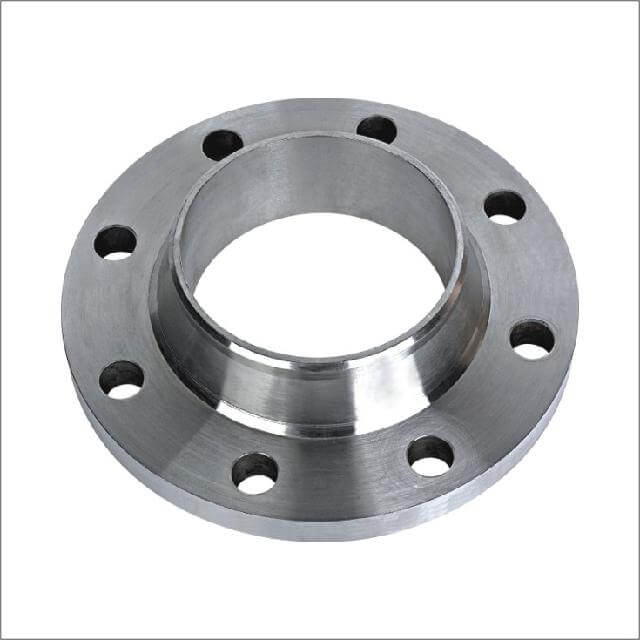
Polymer Sealed Bag Solutions
Sealed bags can be completely wrapped up the flange, the composition is composed of low permeability polymer, corrosion inhibitor steam and desiccant composition. It is easy to install, but the two ends of the bag are sealed with tape only, rather than using a durable and effective mechanical bond. A large area of vapor space inside the bag, easy to gather a lot of water, corrosion inhibitor will be consumed in a period of time.
A New Type of Peelable Sealing Membrane System
For the flange corrosion problem, the company's use of polymer chemistry, developed a resilient and resilient enough new peelable sealing film system, it can be forced back stripping but will not be torn, with rubber elasticity, And is completely free of isocyanates and toxic metal catalysts.
The system is specifically designed to provide protection for flanges, fasteners and associated piping, and can be bonded to hand-processed substrates without the need for hot work, but is safe and easy to construct.
The system uses corrosion inhibitors as the primer, providing overall corrosion protection, while the coating itself has a strong bond, you can rule out all the water within the system.
System corrosion resistance
The corrosion resistance of the system was evaluated by salt spray testing by evaluating the corrosion resistance of the coating by continuously placing the sample in a salt spray environment. The sodium chloride solution of 5% mass fraction was transformed into high temperature salt spray at 35 ℃. The test specimen is an assembled flange connection with bare steel on one side and a sealant membrane system on one side.
The samples were exposed to the salt spray environment for 1000 h, and no signs of corrosion were observed under the sealing membrane system. In contrast, the other side of the flange of the bare steel part of serious corrosion.
System adhesion performance
In order to ensure that the port can be permanently sealed and remove moisture, the system needs to have excellent adhesion, in particular, with the surface of the surface treatment can be closely attached together. According to ASTM D429 and ISO8510-1, in the manual surface treatment of three different substrates on the adhesion test.